
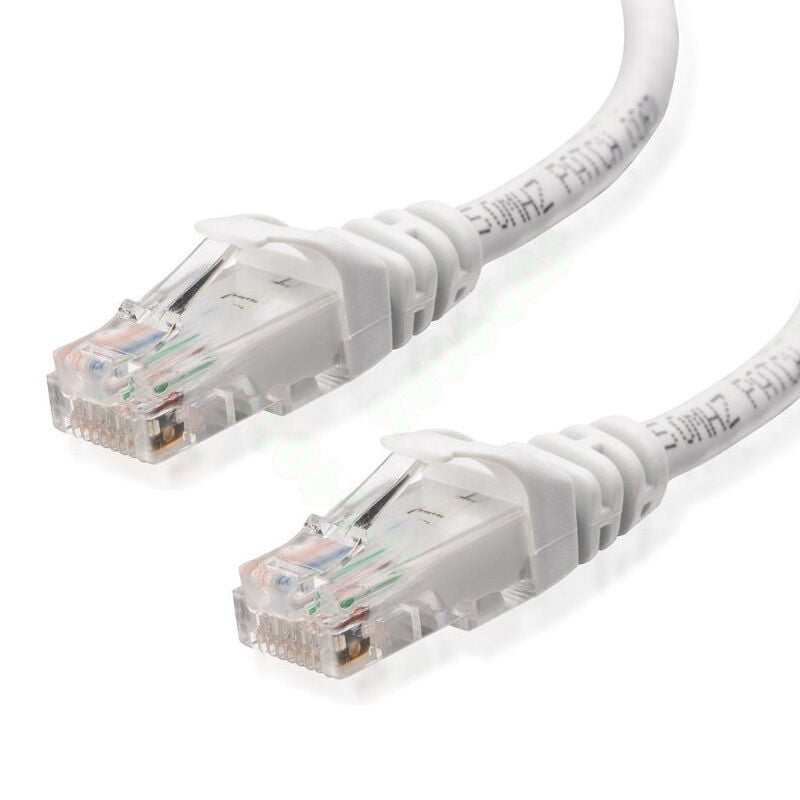
Insert prepped cable into the connector until copper conductors are seated at front of connector housing.Carefully reshape the cable jacket using lineman’s pliers or similar for easier insertion.Push wire bar onto all wires, to 3/16″ from jacket, then cut wires flush with wire bar.Separate and arrange pairs for desired wiring standard, then cut across all wires.Separate the twisted pairs and drain wire ensure that there were no kinks in any of them.Strip the cable jacket about 2 inches, cut foil (if present) to 1/4″ and pull back over jacket.Start with clean hands, cable, parts, tools to avoid electrical irregularities in the finished product Standard connectors will simply not fit these larger cables so specialty connectors and crimp tools must be used instead. To do this the cables must be heavily shielded and large cable jackets must be used. These Cat6A cables are designed to process data at high speeds and thus need to be resistant to RF. The larger and more difficult Cat6A cables to work with require a specific connector design to accommodate the cable jacket size. Since the cable types and termination kits have changed to CAT6A and above, it’s important to revisit how you do termination in the field. When you push the data rate, you’ll see the effects of any termination issues, even if the connections look good. As frequencies increase, demands placed on cable impedance, shielding, grounding, and termination increase as well. Using higher speed data rates, up to 10 Gig now, means you’re even further into radio frequencies. It also contains more protection against interference and signal leakage. It’s attractive for high performance video and audio applications including broadcast television studios, server rooms, and other demanding tasks.
